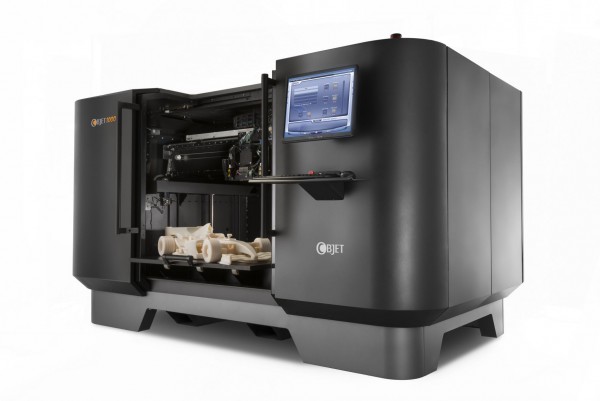
You must have have heard about a new device creating 3-d solid objects using digital technology. This devices is called 3-d printers and can “print” in plastic,metal, nylon, and over a hundred other materials. It can be used for making nonsensical little models like the over-printed Yoda, yet it can also print manufacturing prototypes, end user products, quasi-legal guns, aircraft engine parts and even human organs using a person’s own cells.
3-D printing or additive manufacturing is a process of making three dimensional solid objects from a digital file. The creation of a 3D printed object is achieved using additive processes. In an additive process an object is created by laying down successive layers of material until the entire object is created. Each of these layers can be seen as a thinly sliced horizontal cross-section of the eventual object.
How it works
It all starts with making a virtual design of the object you want to create. This virtual design is made in a CAD (Computer Aided Design) file using a 3D modeling program (for the creation of a totally new object) ór with the use of a 3D scanner (to copy an existing object). This scanner makes a 3D digital copy of an object and puts it into a 3D modeling program.
To prepare the digital file created in a 3D modeling program for printing, the software slices the final model into hundreds or thousands of horizontal layers. When this prepared file is uploaded in the 3-D printer, the printer creates the object layer by layer. The 3-D printer reads every slice (or 2D image) and proceeds to create the object blending each layer together with no sign of the layering visible, resulting in one three dimensional object.
Methods and technologies
Not all 3-D printer use the same technology to realize their objects. There are several ways to do it and all those available as of 2012 were additive, differing mainly in the way layers are build to create the final object. Some methods use melting or softening material to produce the layers. Selective laser sintering (SLS) and fused deposition modeling (FDM) are the most common technologies using this way of printing. Another method of printing is to lay liquid materials that are cured with different technologies. The most common technology using this method is called stereolithography (SLA).
Selective laser sintering (SLS)
This technology uses a high power laser to fuse small particles of plastic, metal, ceramic or glass powders into a mass that has the desired three dimensional shape. The laser selectively fuses the powdered material by scanning the cross-sections (or layers) generated by the 3D modeling program on the surface of a powder bed. After each cross-section is scanned, the powder bed is lowered by one layer thickness. Then a new layer of material is applied on top and the process is repeated until the object is completed.
All untouched powder remains as it is and becomes a support structure for the object. Therefore there is no need for any support structure which is an advantage over SLS and SLA. All unused powder can be used for the next printing. SLS was developed and patented by Dr. Carl Deckard at the University of Texas in the mid-
1980s, under sponsorship of DARPA.
Fused deposition modeling (FDM)
The FDM technology works using a plastic filament or metal wire which is unwound from a coil and supplies material to an extrusion nozzle which can turn the flow on and off. The nozzle is heated to melt the material and can be moved in both horizontal and vertical directions by a numerically controlled mechanism, directly controlled by a computer-aided manufacturing (CAM) software package. The object is produced by extruding melted material to form layers as the material hardens immediately after extrusion from the nozzle.
FDM was invented by Scott Crump in the late 80’s. After patenting this technology he started the company Stratasys in 1988. The software that comes with this technology automatically generates support structures if required. The machine dispenses two materials, one for the model and one form a disposable support structure.
The term fused deposition modeling and its abbreviation to FDM are trademarked by Stratasys Inc. The exactly equivalent term, fused filament fabrication (FFF), was coined by the members of the RepRap project to give a phrase that would be legally unconstrained in its use.
Stereolithography (SLA)
The main technology in which photopolymerization is used to produce a solid part from a liquid is SLA. This technology employs a vat of liquid ultraviolet curable photopolymer resin and an ultraviolet laser to build the object’s layers one at a time. For each layer, the laser beam traces a cross-section of the part pattern on the surface of the liquid resin. Exposure to the ultraviolet laser light cures and solidifies the pattern traced on the resin and joins it to the
layer below.
After the pattern has been traced, the SLA’s elevator platform descends by a distance equal to the thickness of a single layer, typically 0.05 mm to 0.15 mm (0.002″ to 0.006″). Then, a resin-filled blade sweeps across the cross section of the part, re-coating it with fresh material. On this new liquid surface, the subsequent layer pattern is traced, joining the previous layer. The complete three dimensional object is formed by this project. Stereolithography requires the use of supporting structures which serve to attach the part to the elevator
platform.
This technique was invented in 1986 by Charles Hull, who also at the time founded the company, 3D Systems
Personal 3-D Printer
So far we’ve only talked about commercial 3-D printer. There is a whole other world of 3-D printers: personal and DIY hobbyist models. And they are getting cheap, with prices typically in the range of $300 – $2,000.
The RepRap open source project really ignited this hobbyist market in the same way the Apple I microcomputer ignited the hobbyist desktop computer market in the late 1970s. For about a thousand dollars, people have been able to buy the RepRap kit and put together their own personal 3-D printer, complete with any customizations they were capable of making. And what’s more, these printers print most of the parts for more printers. RepRap is short for replicating rapid prototyper, so complete self-replication, including electronic circuit boards, is the goal.
The interest in RepRap spawned scores of other low-cost 3-D printer, both DIY and fully-assembled, and as the prices keep coming down, it puts 3-D printer into more and more and more hands.
But do you have to be an engineer or a 3D modeling expert to create 3D models on your own 3D printer? No, not at all. While complex and expensive CAD software like AutoCAD and Solidworks have a steep learning curve, there are a number of other programs, many free, that are very easy to learn. The free version of Google SketchUp, for example, is very popular for its ease of use; and the free Blender program is popular for its advanced features.
If you don’t have your very own 3-D printer, not to worry, there are 3-D printing service bureaus like Shapeways and Ponoko that can very inexpensively print and deliver an object from a digital file that you simply upload to their user-friendly website. It’s almost as easy as ordering a custom t-shirt from Cafepress or Zazzle.
Even if you don’t design your own 3D model, you can still print some very cool pieces. There are model repositories such as Thingiverse, 3D Parts Database, and 3D Warehouse that have model files you can download for free.
What do all these people print? It’s limitless. Some print things like jewelry, some print replacement parts for appliances such as their dishwasher, some invent all sorts of original things, some create art, and some make toys for their kids. With the many types of metal, plastic, glass, and other materials available (even gold and silver), just about anything can be printed.
Still want to know more about 3-d printer, comment below